What We Offer
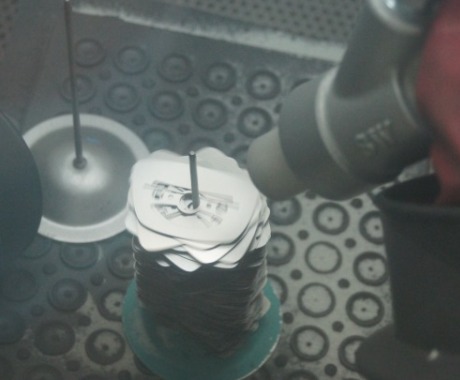
Sandblasting
The mixture of abrasive material and water is transported through a pump, and the force of compressed air is used to spray it on the workpiece for surface treatment.
Best Service
We have been engaged in precision metal laser cutting for many years, with many years of professional technology and experience. To provide you with the best service.
Process Integration
After discussions between senior designers and customers, integrate metal or composite material technology to create success together.
Quick Reply
With a professional design team and production team, discuss and confirm through the customer's drawings, and reply within three working days at the earliest.
Dry Sandblasting
Using abrasive materials and compressed air as power through a vacuum tube to accelerate the blasting, or using a hoist to move it onto a high-speed turntable to throw the sand material onto the workpiece with centrifugal force, or through a spray gun, connecting a sand supply tube before the air outlet with high-pressure air to carry the sand material together and treat the surface of the workpiece. This process treats the metal surface into a matte state, improves adhesion, removes gilding, deoxidation layer, adjusts the friction coefficient, and then undergoes subsequent coloring (such as: baking paint) process. Its biggest feature is that because it is dry, it does not need to be dried, and there is no worry about rust.
Wet Sandblasting
The mixture of abrasive material and water is transported through a pump, and the force of compressed air is used to spray it on the workpiece for surface treatment. During the sandblasting process, glass sand is added to make the metal surface not completely matte, and mixed with reflections like pearl light, which can improve adhesion, remove and clean surface adhesions, adjust the friction coefficient, and then undergo subsequent coloring (such as: PVD) process. Because it is a wet process, finer abrasive materials can be used, which is most suitable for processing complex-shaped workpieces. The biggest feature is the use of fine abrasive materials, which is more suitable for processing complex-shaped precision workpieces compared to dry sandblasting.